Product Packaging Manufacturing BUNDLE
Are you tracking Product Packaging KPIs to boost your manufacturing's performance? Critical metrics like Manufacturing Efficiency Metrics and Financial KPIs for Manufacturing reveal hidden opportunities for enhanced productivity.
Do you know which 5 Essential KPIs can transform your operational strategy? Discover actionable insights and optimize processes with our Product Packaging Manufacturing Business Plan Template to drive exceptional results.
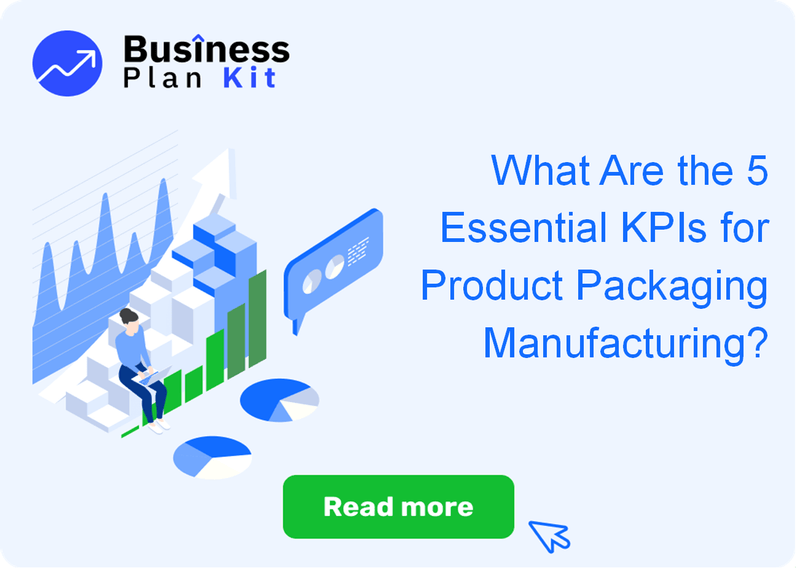
# | KPI Name | Description |
---|---|---|
1 | Production Efficiency | Measures the ratio of actual output to potential output to reflect resource utilization and process improvements. |
2 | Material Waste Percentage | Calculates the percentage of raw materials wasted to identify process improvements and reduce environmental impact. |
3 | Order Fulfillment Rate | Assesses the percentage of customer orders completed on time and in full, enhancing customer satisfaction. |
4 | Labor Cost Percentage | Measures total labor costs as a percentage of revenue to optimize staffing levels and productivity. |
5 | Customer Satisfaction Index | Evaluates overall customer satisfaction through feedback to drive repeat business and loyalty. |
Key Takeaways
- Tracking KPIs gives you real-time insights into both financial health and operational efficiency.
- Understanding financial metrics such as gross profit, net profit, and EBITDA is key to assessing profitability.
- Operational KPIs like production efficiency and labor cost percentage help optimize processes and resource allocation.
- Customer-centric metrics such as the Customer Satisfaction Index and order fulfillment rate drive longer-term growth and loyalty.
Why Do Product Packaging Manufacturing Need to Track KPIs?
Empower your Product Packaging Manufacturing with a clear view of your financial health and operational efficiency using essential KPIs. These metrics help you identify cost inefficiencies, optimize material waste reduction, and drive strategic production improvements. Leverage data-driven decision making to boost investor confidence and improve your operational KPIs. Discover more insights in How to Start a Successful Product Packaging Manufacturing Business?
Essential Manufacturing KPIs
- Product Packaging KPIs provide real-time insights into financial KPIs for manufacturing like a steady net profit margin and effective cash flow management.
- Manufacturing Efficiency Metrics help monitor production line performance, ensuring material usage is optimized and order fulfillment rate reaches above 95%.
- Operational KPIs reveal opportunities for labor cost optimization and grease cost reduction by as much as 10%, streamlining overall production.
- Customer-Centric KPIs boost customer satisfaction through improved Net Promoter Score (NPS) and robust customer retention strategies.
What Financial Metrics Determine Product Packaging Manufacturing’s Profitability?
Empower your decision-making by understanding the key financial metrics that drive profitability in product packaging manufacturing. Grasping the differences between gross profit, net profit and EBITDA is essential for refining your pricing strategies and production efficiency. Analyzing these Financial KPIs for Manufacturing – including COGS, break-even points, and cash flow metrics – ensures you stay ahead with robust data-driven insights. Learn more about this critical investment by exploring How Much Does It Cost to Start a Product Packaging Manufacturing Business?.
Key Financial Metrics
- Gross Profit in Manufacturing analysis pinpoints how operational costs and COGS affect margins.
- Net Profit and EBITDA comparisons reveal the true profitability and performance of your operations.
- Break-Even Analysis and Cash Flow Management are crucial to maintain sustainable manufacturing efficiency.
- Measuring Revenue per Production Hour alongside pricing strategies enhances production line monitoring and overall operational KPIs.
How Can Operational KPIs Improve Product Packaging Manufacturing Efficiency?
Operational KPIs empower you to optimize every facet of your product packaging manufacturing. By tracking key metrics like production line efficiency and labor cost percentage, you can pinpoint areas for improvement. This approach not only boosts productivity but also drives effective cash flow management and labor cost optimization. Discover How to Start a Successful Product Packaging Manufacturing Business? for detailed strategies.
Essential Operational Insights
- Production Line Monitoring: Track efficiency to maximize output and improve overall manufacturing efficiency metrics.
- Labor Cost Management: Use labor cost percentage to optimize staff productivity, ensuring costs remain below 15% of the revenue.
- Material Waste Reduction: Monitor material waste and inventory turnover to reduce losses by up to 20%.
- Order Accuracy & Cycle Times: Measure order fulfillment rate and production cycle times to achieve a consistent quality standard.
- Daily Output Analysis: Evaluate daily output per labor hour to refine staffing levels and drive efficiency gains.
What Customer-Centric KPIs Should Product Packaging Manufacturing Focus On?
Empower your packaging operations by focusing on key customer-centric KPIs that drive loyalty and operational efficiency. At PackageWise Solutions, tracking metrics like customer retention and Net Promoter Score (NPS) has proven vital for maintaining a competitive edge in sustainable packaging. By tightening your Manufacturing Efficiency Metrics and monitoring financial KPIs such as Cash Flow Management, you can optimize spending and enhance customer satisfaction. Discover details such as How Much Does It Cost to Start a Product Packaging Manufacturing Business? to take your business strategy further.
Customer-Centric Performance Metrics
- Track customer retention rate to gauge repeat business and ensure consistent revenue, with ideal benchmarks approaching 85%.
- Measure Net Promoter Score (NPS) as a core indicator of brand loyalty; scores above 50 suggest robust word-of-mouth potential.
- Monitor customer feedback and satisfaction ratings to manage your reputation effectively and drive continuous improvement in Operational KPIs.
- Evaluate average order size and upsell effectiveness, key for refining your Product Packaging KPIs and reducing Customer Acquisition Cost (CAC).
How Can Product Packaging Manufacturing Use KPIs to Make Better Business Decisions?
Empower your product packaging manufacturing process with data-driven KPIs to drive strategic growth. Aligning Product Packaging KPIs with long-term goals offers clarity on where cost cuts and efficiency improvements are needed. Dive into real metrics to optimize pricing, reduce costs, and boost both customer satisfaction and operational excellence. For instance, integrating smart KPIs has helped companies reduce labor costs by over 15% while improving overall production efficiency.
Key KPI Strategies
Align KPIs with long-term growth and sustainability goals to drive strategic decisions. Utilize data-driven insights, from Cash Flow Management to pricing strategies, to reduce costs and boost Gross Profit in Manufacturing (Learn More). Integrate Manufacturing Efficiency Metrics in staff training, scheduling, and labor cost control to enhance production line monitoring. Leverage Customer-Centric KPIs, such as the Net Promoter Score (NPS), to refine marketing campaigns and improve retention, ensuring continuous KPI tracking for competitive edge.
What Are 5 Core KPIs Every Product Packaging Manufacturing Should Track?
KPI 1: Production Efficiency
Definition
Production Efficiency is a key manufacturing efficiency metric that measures the ratio of actual output to the maximum potential output. It is essential for Product Packaging KPIs as it reflects how well your resources and time are being utilized.
You can learn more about improving production efficiency to ensure you stay competitive and reduce costs.
Advantages
- Optimizes resource use: Ensures machines and labor are effectively utilized, which is vital for operational KPIs.
- Improves decision-making: Provides insights on machine downtime and labor productivity, supporting data-driven strategies.
- Reduces costs: By closely monitoring production efficiency, you can implement process improvements that trim financial KPIs for manufacturing.
Disadvantages
- Single-dimensional view: Relying solely on production efficiency may overlook quality issues.
- Data sensitivity: Machine downtime or unplanned stoppages can skew the efficiency metrics.
- Overemphasis risk: Focusing too much on efficiency might compromise other Product Packaging KPIs like the order fulfillment rate.
Industry Benchmarks
In the packaging manufacturing industry, an efficiency rate of 85% or above is typically considered excellent, while values below 70% might indicate underutilization of resources. Benchmarking against these industry standards helps maintain a competitive lead time and align with supply chain efficiency.
How To Improve
- Implement regular maintenance to minimize machine downtime.
- Enhance labor cost optimization through targeted training and process improvements.
- Deploy real-time production line monitoring for prompt corrective actions.
How To Calculate
Calculate Production Efficiency using the formula below. This financial KPI for manufacturing provides a clear quantitative measure of your actual production performance compared to the maximum potential.
Example of Calculation
If PackageWise Solutions has a maximum production capacity of 1,000 units per day and produces 850 units, the Production Efficiency is calculated as follows:
This demonstrates effective use of resources and serves as a benchmark for continuous improvement. To explore further insights, check out How Much Does a Product Packaging Manufacturing Owner Earn?
Tips and Trics
- Monitor machine downtime closely to anticipate potential disruptions.
- Regularly train staff to drive labor cost optimization and boost productivity.
- Leverage data-driven decision making by integrating resource tracking tools.
- Compare your production figures against industry benchmarks, aiming for efficiency around 85% to remain competitive.
KPI 2: Material Waste Percentage
Definition
This KPI calculates the percentage of raw materials wasted during production, helping you monitor process efficiency. It plays a crucial role in evaluating your operational performance by identifying how much material does not convert into finished product.
Advantages
- Optimizes Usage: Highlights inefficient areas, enabling targeted improvements to reduce waste.
- Boosts Sustainability: Supports recycling and reuse initiatives, vital for eco-friendly operations.
- Enhances Efficiency: Provides actionable insights to improve production planning and quality control.
Disadvantages
- Limited Scope: Does not capture issues outside raw material usage like energy efficiency.
- Data Dependency: Requires precise input data, and inaccuracies can lead to misinterpretation.
- Complex Interactions: Can be influenced by external factors such as variable supplier quality.
Industry Benchmarks
In the packaging manufacturing industry, a Material Waste Percentage typically ranges from 2% to 5%. Staying below these values signifies efficient production planning and quality control, a critical insight for businesses like PackageWise Solutions.
How To Improve
- Enhance production planning and workflow management to minimize off-cuts.
- Invest in rigorous quality control and supplier audits to ensure material consistency.
- Adopt lean manufacturing techniques to streamline operations and reduce waste.
How To Calculate
Determine the percentage of wasted material by dividing the total waste by the initially supplied raw material, then multiply the result by 100. This calculation helps in identifying losses during production.
Example of Calculation
For example, if your production line starts with 1000 kg of raw materials and produces 30 kg of waste, calculate the KPI as follows:
This standard calculation provides a clear indicator of how efficiently you use materials, aligning with best practices in Product Packaging KPIs and Manufacturing Efficiency Metrics.
Tips and Trics
- Regularly monitor waste outputs to swiftly identify process bottlenecks.
- Integrate data-driven decision making to adjust production workflows effectively.
- Collaborate with suppliers to ensure consistently high raw material quality.
- Use production line monitoring systems to track waste in real-time and implement quick corrective actions.
For additional insights on reducing waste, Explore ways to reduce material waste and find more strategies on How to Start a Successful Product Packaging Manufacturing Business?
KPI 3: Order Fulfillment Rate
Definition
The Order Fulfillment Rate measures the percentage of customer orders that are completed on time and in full. It serves as a key indicator of operational performance by revealing supply chain efficiency, inventory management success, and production scheduling effectiveness.
Advantages
- Enhances customer satisfaction and loyalty by ensuring timely delivery.
- Improves operational efficiency through better production and inventory management.
- Strengthens your market reputation and provides a competitive edge.
Disadvantages
- May not fully capture quality issues within fulfilled orders.
- Can be impacted by seasonal fluctuations and unforeseen supply chain disruptions.
- Requires robust data collection from various operational systems for meaningful insights.
Industry Benchmarks
In the product packaging manufacturing sector, achieving an order fulfillment rate of 95% or higher is common among leading companies. High-performing manufacturers often push beyond 98% as they streamline processes using advanced ERP systems and improved production scheduling.
How To Improve
- Optimize your supply chain for efficiency by integrating advanced production line monitoring.
- Implement real-time order tracking to quickly address delays and discrepancies.
- Enhance production scheduling and inventory management to reduce bottlenecks.
How To Calculate
Calculate the Order Fulfillment Rate by dividing the number of orders completed on time by the total number of orders, then multiplying by 100 to get a percentage.
Example of Calculation
For instance, if PackageWise Solutions fulfills 980 orders on time out of a total of 1,000, the Order Fulfillment Rate is calculated as follows:
This high percentage demonstrates effective production scheduling and supply chain efficiency, leading to enhanced customer satisfaction. To further explore ways to improve your operational metrics, explore additional resources on managing and optimizing your production processes.
Tips and Trics
- Regularly monitor your production lines using real-time data to preempt delays.
- Invest in technology, such as ERP systems, to integrate inventory and order management.
- Benchmark your order fulfillment against industry standards to set realistic targets.
- Utilize customer feedback to refine supply chain and production processes; for more insight, check How Much Does It Cost to Start a Product Packaging Manufacturing Business?
KPI 4: Labor Cost Percentage
Definition
Labor Cost Percentage measures total labor costs as a percentage of revenue. It is a key financial KPI for manufacturing that helps you balance staffing levels with profitability and productivity.
Advantages
- Helps maintain an optimal workforce size to drive manufacturing efficiency metrics.
- Identifies inefficiencies in labor utilization, aiding in labor cost optimization.
- Improves decision-making by linking employee productivity with overall profitability.
Disadvantages
- May be skewed by unexpected overtime or irregular shifts.
- Fluctuations in production scheduling can affect the consistency of the metric.
- High staff turnover can make it challenging to benchmark effectively over time.
Industry Benchmarks
In product packaging manufacturing, a typical benchmark for Labor Cost Percentage is between 20% and 30% of total sales. These values are essential for comparing your operational efficiency against the industry standard.
How To Improve
- Monitor overtime trends and adjust shift scheduling to minimize excess costs.
- Invest in training programs to boost workforce productivity and reduce errors.
- Utilize modern production line monitoring for real-time insights into staff performance; optimize labor costs effectively.
How To Calculate
Calculate Labor Cost Percentage by dividing total labor costs by total revenue and multiplying by 100 to obtain a percentage.
Example of Calculation
For example, if your total labor costs are $50,000 and your total revenue is $200,000, the calculation is as follows:
This means 25% of your revenue is dedicated to labor costs, aligning with industry standards for many manufacturing operations.
Tips and Trics
- Track daily labor hours for precision and timely adjustments.
- Deploy automated production line monitoring systems to capture real-time data.
- Regularly evaluate staff turnover rates to understand cost fluctuations.
- Compare against proven benchmarks and read How Much Does a Product Packaging Manufacturing Owner Earn? for further insights.
KPI 5: Customer Satisfaction Index
Definition
The Customer Satisfaction Index measures overall customer approval by aggregating survey responses and feedback. In product packaging manufacturing, it tracks customers’ perceptions about product quality, delivery reliability, and customer service.
Advantages
- Drives repeat business and strengthens brand loyalty.
- Provides actionable feedback to enhance product and service quality.
- Supports data-driven decision-making to improve long-term profitability.
Disadvantages
- Can be subject to biased or inconsistent survey responses.
- May lag behind actual service issues due to survey frequency.
- Interpreting qualitative feedback often requires deeper analysis.
Industry Benchmarks
In packaging manufacturing, a benchmark score above 80% is typically seen as excellent. Other manufacturing sectors often have scores ranging from 70% to 90%, highlighting the importance of using this KPI to compare performance across industries.
How To Improve
- Enhance product quality by adopting sustainable practices as done at PackageWise Solutions.
- Streamline delivery logistics to ensure reliability and faster order fulfillment.
- Invest in training customer service teams to respond promptly to feedback.
How To Calculate
Calculate the Customer Satisfaction Index by dividing the total satisfaction score by the number of responses and multiplying by 100 to get a percentage.
Example of Calculation
For instance, if you receive responses from 100 customers with a total score of 850, the Customer Satisfaction Index would be calculated as follows:
Since the scoring is typically on a scale of 1 to 10, the average score of 8.5 translates to an index value of 85%, indicating strong positive sentiment.
Tips and Trics
- Regularly survey customers and monitor trends to identify immediate improvement areas.
- Integrate customer feedback into production decisions to refine quality and delivery.
- Benchmark against industry standards and adjust strategies to maintain a satisfaction rate above 80%.
- Leverage insights from Understand how to boost customer satisfaction for further actionable strategies.
For more strategic insights on launching and growing your packaging business, check out How to Start a Successful Product Packaging Manufacturing Business?