Biodiesel Manufacturing BUNDLE
How much does it cost to start a biodiesel manufacturing business? Are you curious about biodiesel manufacturing startup costs and what factors drive expenses? Discover if advanced technology or feedstock supply costs are the real deal-breakers in this eco-friendly venture.
Are hidden expenses and regulatory compliance challenges stressing you out? Learn how to optimize biodiesel facility setup expenses and manage ongoing operational costs with proven strategies and our Biodiesel Manufacturing Business Plan Template. Ready to power-up your renewable fuel production?
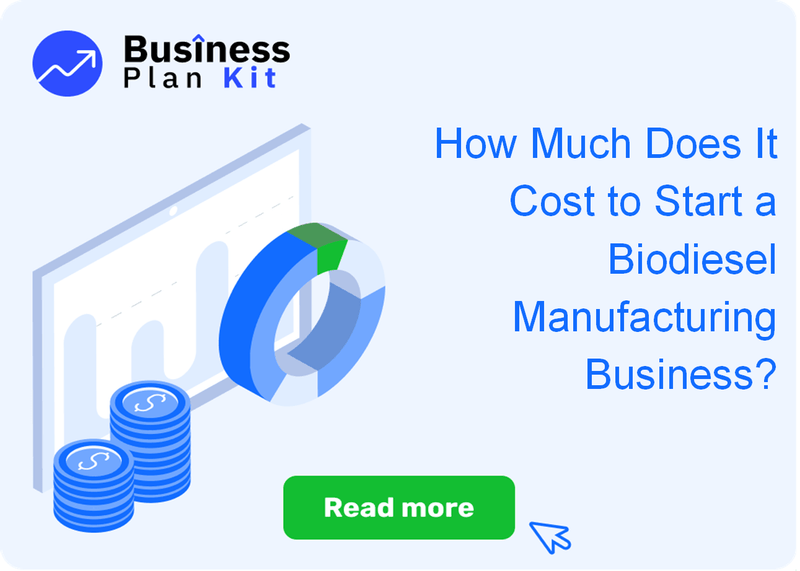
# | Startup Cost | Description | Min Amount | Max Amount |
---|---|---|---|---|
1 | Real Estate & Lease | Securing property with deposits, renovations, and leasing fees based on local benchmarks. | $70,000 - $150,000 | $200,000 - $400,000 |
2 | Production Equipment | Purchasing core biodiesel processing machinery with installation and upgrade costs. | $330,000 - $1,320,000 | $360,000 - $1,440,000 |
3 | Infrastructure Mods | Upgrading facility systems including utilities and safety measures for efficient production. | $50,000 - $150,000 | $60,000 - $180,000 |
4 | Licenses, Permits & Insurance | Obtaining necessary certifications, comprehensive insurance, and compliance-related services. | $25,000 - $95,000 | $28,000 - $105,000 |
5 | Raw Material & Lab Setup | Investing in bulk waste oils, quality lab equipment, and safe storage facilities. | $52,500 - $220,000 | $55,000 - $230,000 |
6 | Staffing & Operations | Recruiting and training skilled personnel and setting up efficient operational systems. | $150,000 - $400,000 | $160,000 - $420,000 |
7 | Marketing & Branding | Developing brand identity and digital presence with targeted public relations and advertising. | $30,000 - $100,000 | $31,500 - $110,000 |
Total | $707,500 - $2,435,000 | $894,500 - $2,885,000 |
Key Takeaways
- Startup costs for a biodiesel manufacturing business can range from $707,500 to $2,885,000, depending on various factors.
- Location and facility size can significantly impact your overall budget, affecting costs by 20–35%.
- Investing in automation may increase initial expenses by 5–10%, but it can lead to long-term operational savings.
- Setting aside 10–15% of your total capital for unexpected expenses is crucial for financial stability.
What Are Main Factors That Influence Biodiesel Manufacturing Startup Costs?
Understanding the key factors that influence biodiesel manufacturing startup costs is crucial for any aspiring entrepreneur in the renewable energy sector. From facility size to technology integration, each element plays a significant role in shaping your financial landscape. Let's dive into the specifics that will help you plan effectively.
Main Factors Influencing Costs
- Location & Size: Facility space can vary from 5,000 to 20,000 square feet, impacting pricing by as much as 20–35% of the overall budget.
- Feedstock Supply: Variability in waste oil availability may demand setting aside 10–15% extra for supply chain stabilization.
- Technology Integration: Cutting-edge conversion equipment and blockchain verification can increase initial costs by 15–25%.
- Regulatory Compliance: EPA standards and local environmental mandates may add an extra 10–20% to startup estimates.
- Scale of Production: Small versus large-scale production affects capital expenditures, seeing differences up to 40% in cost structures.
- Operational Efficiency: Incorporating automation may initially cost 5–10% more but promises long-term savings.
- Strategic Location: Proximity to waste oil suppliers can reduce logistics expenses by 10–15%.
By accounting for these factors, you can create a more accurate biodiesel manufacturing startup costs estimate. For further insights into the financial aspects of running a biodiesel facility, consider exploring How Much Does a Biodiesel Manufacturing Owner Earn?.
What Are Biggest One-Time Expenses When Opening Biodiesel Manufacturing?
Starting a biodiesel manufacturing venture involves several significant one-time expenses that can shape your financial landscape. Understanding these costs is crucial for effective budgeting and planning. Here’s a breakdown of the key expenses you should anticipate.
Key One-Time Expenses
- Facility Purchase or Lease: Expect down payments of 10–20% of property costs; long-term leases require careful negotiation.
- Processing Equipment Installation: Large reactors and filtration systems can range from $200,000 to $1,000,000.
- Technological Infrastructure: Integrating advanced control systems and blockchain modules may add 5–10% to overall costs.
- Safety & Environmental Setup: Initial permits and safety installations can cost between $50,000 and $150,000.
- Engineering & Construction Services: Professional fees often represent 8–12% of capital investments.
- Custom Fabrication: Tailored improvements may incur costs of 10–20% above standard estimates.
- Branding & Marketing Launch: A robust launch campaign might add $30,000 to $100,000 in initial expenses.
It’s essential to account for these biodiesel manufacturing startup costs to ensure a successful launch. For a more detailed exploration of the financial metrics involved, check out What Are the 5 Key Performance Indicators and Metrics for a Successful Biodiesel Manufacturing Business?.
What Are Ongoing Monthly Costs of Running Biodiesel Manufacturing?
Understanding the ongoing monthly costs of running a biodiesel manufacturing operation is crucial for your financial planning. These expenses can significantly impact your profitability, so let’s break down what you need to anticipate.
Key Monthly Expenses
- Facility rent and utilities can range between $5,000 and $20,000, depending on size and energy needs.
- Labor and staffing costs typically account for 15–30% of operating expenses, averaging $50,000 to $200,000 monthly.
- Feedstock procurement may consume 30–40% of your production expenses; for a detailed overview see comprehensive breakdown.
- Equipment maintenance could take up 5–10% of monthly revenues, ensuring your machinery runs smoothly.
- Software subscriptions for blockchain tracking and operational management steadily add to your recurring charges.
- Regulatory compliance expenses may contribute an extra 2–5% to monthly costs due to regular audits and permits.
- Administrative operations round out your financial plan, including ongoing office and operational expenses.
Keeping a close eye on these biodiesel operational expenses will help you maintain a sustainable and profitable business. For further insights, check out How Much Does a Biodiesel Manufacturing Owner Earn?.
How Can You Prepare for Hidden and Unexpected Expenses?
Preparing for hidden and unexpected expenses is crucial in the biodiesel manufacturing industry. By anticipating these costs, you can better manage your budget and ensure the sustainability of your operation. Let's dive into the strategies that will help you stay ahead of financial surprises.
Strategies to Mitigate Unexpected Costs
- Establish an emergency fund of 10–15% of total capital to cover unforeseen expenses.
- Prepare for equipment breakdowns, which can cost up to $10,000 per incident.
- Stay informed about regulatory adjustments that may require additional spending; see government insights.
- Plan for supply chain disruptions that could incur premium costs of 5–10% on raw materials.
- Account for market fluctuations in feedstock pricing, which could impact your budget by 10–20%.
- Consider potential increases in insurance fees due to new legal requirements, potentially rising by 3–5% annually.
- Prepare for technology upgrades that may lead to additional capital expenditures.
For more insights on budgeting and managing expenses, check out How to Start a Successful Biodiesel Manufacturing Business?.
What Are Common Pitfalls When Estimating Biodiesel Manufacturing Startup Costs?
Estimating biodiesel manufacturing startup costs can be tricky. Avoiding common pitfalls will help you budget effectively and secure funding for your venture. Here are key areas where mistakes often happen that can impact your financial planning.
Key Pitfalls to Avoid
- Underestimating permitting fees can inflate budgets by 5–15%; see this extension report for benchmarks.
- Ignoring future maintenance costs may lead to a 10–20% increase in expenses later.
- Overlooking labor variability can unexpectedly elevate payroll budgets by 10–15%.
- Misjudging equipment installation costs can add an extra 8–12% to base expenses.
- Failing to account for technological integration might overrun by 5–10%.
- Underpreparing for regulatory audits can lead to unexpected spending spikes.
- Inadequate contingency planning, typically 10–15%, leaves gaps for unplanned expenditures.
For more detailed insights on how to navigate these challenges, check out How to Start a Successful Biodiesel Manufacturing Business?.
What Are Biodiesel Manufacturing Startup Costs?
Startup Cost 1: Real Estate & Lease Costs
Understanding real estate and lease costs is crucial for your biodiesel manufacturing business. These expenses can significantly impact your overall startup budget, often accounting for a substantial portion of your initial investment. With costs varying based on location and facility size, it’s essential to accurately estimate these expenses to ensure financial viability.
Key Cost Drivers
The primary cost drivers for real estate and lease expenses include the size of the facility, location premiums, and necessary renovations. Each of these factors can lead to significant variations in your overall budget.
Factors Affecting Cost
- Security deposits typically require 5–15% of total property cost.
- Lease agreements are often structured for 3–5 years with periodic escalations.
- Renovation or retrofitting expenses can add 10–25% to initial costs.
- Location premiums in industrial zones often reflect higher costs per square foot.
Potential Cost Savings
Implementing strategic cost-saving measures can significantly reduce your real estate expenses. By carefully selecting your location and negotiating lease terms, you can optimize your budget.
- Negotiate longer lease terms for better rates.
- Consider shared facilities to lower costs.
- Explore government incentives for renewable energy businesses.
- Utilize virtual tours to minimize travel costs during site selection.
- Research local market trends to find competitive rates.
- Evaluate multiple locations to find the best deal.
- Plan renovations strategically to avoid unnecessary expenses.
- Engage a real estate consultant for expert negotiation.
Biodiesel Facility Lease and Purchase Cost Breakdown
Expense Component | Estimated Cost | Notes |
---|---|---|
Security Deposits | $3,500 - $15,000 | 5–15% of total property cost |
Lease Agreements | $7 - $15 per square foot | Based on local benchmarks |
Renovation Costs | $7,000 - $50,000 | 10–25% of initial costs |
Startup Cost 2: Production Equipment & Processing Machinery
When launching a biodiesel manufacturing business, the cost of production equipment and processing machinery is a critical factor that can significantly impact your overall startup budget. This expense typically ranges from $300,000 to $1,200,000, depending on the scale and technology of your operation. Understanding these costs is essential for accurate financial planning and ensuring your facility is equipped to meet production demands.
Core Equipment Costs
The primary cost drivers for production equipment include the type of machinery required for biodiesel conversion and the associated installation services. These costs can vary widely based on the technology you choose and the scale of your production.
Factors Affecting Cost
- Type of biodiesel processing machinery selected
- Installation services, which can add 10–20% to equipment expenses
- Custom fabrication requirements that may extend lead times and budgets
- Energy-efficient systems that typically carry a 5–15% premium cost
Potential Cost Savings
To manage your biodiesel equipment installation costs effectively, consider strategies that can lead to significant savings. By planning ahead and exploring various options, you can optimize your budget and enhance operational efficiency.
- Negotiate bulk purchase agreements with suppliers
- Consider leasing equipment instead of purchasing
- Invest in maintenance contracts for long-term savings
- Utilize energy-efficient technologies to reduce operational costs
- Explore grants or subsidies for renewable energy projects
- Implement a phased approach to equipment upgrades
- Research used equipment options to lower initial costs
- Engage with industry networks for shared resources and insights
Biodiesel Production Equipment Cost Breakdown
Expense Component | Estimated Cost | Notes |
---|---|---|
Core Machinery | $300,000 - $1,200,000 | Includes biodiesel processing units and reactors. |
Installation Services | $30,000 - $240,000 | Installation costs can add 10-20% to equipment expenses. |
Energy-Efficient Systems | $15,000 - $180,000 | Premium costs for energy-efficient upgrades. |
Startup Cost 3: Infrastructure & Facility Modifications
Upgrading your plant's infrastructure is a critical aspect of launching a biodiesel manufacturing business. These modifications not only ensure compliance with safety regulations but also enhance operational efficiency. Typically, you should allocate 5–10% of your overall capital for these essential upgrades.
Primary Cost Drivers
The primary cost drivers for infrastructure modifications include the need for electrical, plumbing, and ventilation improvements. Additionally, environmental safety systems, such as spill containment, are crucial for compliance and operational integrity.
Factors Affecting Cost
- Quality of materials used for upgrades
- Local labor rates for installation
- Complexity of safety and environmental systems
- Facility layout optimization needs
Potential Cost Savings
Implementing strategic planning can lead to significant cost savings in infrastructure modifications. By optimizing facility layout and leveraging local resources, you can reduce unnecessary expenses.
- Utilize local contractors for competitive pricing
- Invest in energy-efficient systems to lower utility costs
- Plan upgrades during off-peak seasons for better rates
- Explore grants for renewable energy projects
- Negotiate bulk purchasing for materials
- Implement phased upgrades to spread costs
- Incorporate modular designs for flexibility
- Regularly review and adjust maintenance contracts
Biodiesel Facility Infrastructure Cost Breakdown
Expense Component | Estimated Cost | Notes |
---|---|---|
Electrical Upgrades | $10,000 - $30,000 | Essential for meeting production demands |
Plumbing Improvements | $5,000 - $15,000 | Critical for operational efficiency |
Ventilation Systems | $15,000 - $50,000 | Compliance with safety regulations |
Environmental Safety Systems | $20,000 - $60,000 | Includes spill containment measures |
Facility Layout Optimization | $5,000 - $20,000 | Improves production flow |
Professional Assessments | $3,000 - $10,000 | For structural modifications |
Startup Cost 4: Licenses, Permits, and Insurance
Licenses, permits, and insurance are crucial components of your biodiesel manufacturing startup costs. These expenses can significantly impact your budget, ranging from $20,000 to $80,000 for initial permits and certifications alone. Navigating the regulatory landscape can be challenging, especially for first-time entrepreneurs, as compliance requirements often vary by location and can lead to unexpected costs.
Cost Drivers
The primary cost drivers for licenses, permits, and insurance include the type of certifications required, local regulatory fees, and the complexity of compliance processes. Understanding these factors is essential for accurate budgeting.
Factors Affecting Cost
- Initial permits and environmental certifications
- Comprehensive insurance packages
- Local and state filing fees
- Legal advisory services for compliance
Potential Cost Savings
To manage your licenses, permits, and insurance costs effectively, consider strategies that can help minimize these expenses. By planning ahead and leveraging available resources, you can achieve significant savings.
- Research local regulations to avoid unnecessary fees
- Bundle insurance policies for discounts
- Utilize online resources for permit applications
- Consult with experts to streamline compliance processes
- Negotiate with legal advisors for better rates
- Stay updated on regulatory changes to avoid penalties
- Consider group insurance plans for cost efficiency
- Implement a proactive compliance strategy to reduce risks
Biodiesel Manufacturing Licenses and Permits Cost Breakdown
Expense Component | Estimated Cost | Notes |
---|---|---|
Initial Permits | $20,000 - $80,000 | Cost varies based on local regulations and environmental requirements. |
Insurance Packages | $5,000 - $15,000 | Annual costs depend on coverage levels and business size. |
Legal Advisory Services | 5-10% of total compliance costs | Essential for navigating complex regulations. |
Startup Cost 5: Initial Raw Material Inventory & Lab Setup
Establishing a biodiesel manufacturing business requires a well-planned initial raw material inventory and lab setup. This expense is crucial as it directly impacts your production capabilities and quality assurance processes. Entrepreneurs often face challenges in accurately estimating these costs, which can range significantly based on feedstock availability and lab requirements.
Cost Drivers
The primary cost drivers for initial raw material inventory and lab setup include the bulk purchasing of waste oils, quality assurance testing, and the establishment of safe storage facilities. These elements are essential for maintaining production efficiency and compliance with environmental standards.
Factors Affecting Cost
- Bulk purchasing of waste oils typically requires an investment between $50,000 and $200,000.
- Quality assurance testing and laboratory certifications are necessary expenditures that ensure product quality.
- Proper storage facilities must be established to handle raw materials safely, adding to the initial setup costs.
- Long-term contracts for feedstock can provide discounts, helping to manage overall costs effectively.
Potential Cost Savings
Implementing strategic cost-saving measures can significantly reduce initial expenses related to raw material inventory and lab setup. By leveraging long-term contracts and optimizing lab equipment purchases, you can enhance your budget efficiency.
- Negotiate long-term contracts for feedstock to secure lower prices.
- Invest in energy-efficient lab equipment for long-term savings.
- Utilize local suppliers to minimize transportation costs.
- Implement a just-in-time inventory system to reduce storage expenses.
- Explore grants or subsidies for renewable energy projects to offset costs.
- Conduct bulk purchases to take advantage of economies of scale.
- Regularly review and optimize lab processes to enhance efficiency.
- Consider shared laboratory facilities to reduce initial setup costs.
Biodiesel Raw Material & Lab Setup Cost Breakdown
Expense Component | Estimated Cost | Notes |
---|---|---|
Bulk Waste Oils | $52,500 - $220,000 | Initial investment for feedstock procurement. |
Quality Assurance Testing | $5,000 - $15,000 | Essential for meeting product standards. |
Storage Facilities | $10,000 - $30,000 | Setup costs for safe handling of materials. |
Lab Equipment Upgrades | $2,500 - $10,000 | Improvements to enhance testing capabilities. |
Startup Cost 6: Staffing, Training & Operational Setup
Recruiting and training skilled personnel is a critical component of launching your biodiesel manufacturing business. This expense can consume 20–30% of your initial capital, making it essential to budget effectively. As you build your team, consider the unique challenges of attracting qualified technicians in the renewable energy sector, which can be competitive and demanding.
Cost Drivers
The primary cost drivers for staffing and operational setup include competitive salaries, comprehensive training programs, and onboarding expenses. These factors can significantly impact your overall budget.
Factors Affecting Cost
- Recruitment of skilled technicians and operators
- Comprehensive training programs for compliance and efficiency
- Onboarding and certification fees
- Background checks and recruitment agency fees
Potential Cost Savings
Implementing strategic cost-saving measures can help manage your staffing and operational expenses effectively. Focus on optimizing recruitment processes and investing in employee retention strategies.
- Utilize online platforms for recruitment to reduce agency fees
- Implement in-house training programs to lower training costs
- Offer competitive salaries to retain experienced staff
- Streamline onboarding processes to save time and resources
- Encourage continuous professional development to enhance staff skills
- Leverage workforce management systems to optimize operations
- Negotiate bulk training contracts for cost efficiency
- Consider remote training options to minimize travel expenses
Biodiesel Staffing and Operational Cost Breakdown
Expense Component | Estimated Cost | Notes |
---|---|---|
Recruitment Costs | $30,000 - $100,000 | Includes advertising and agency fees |
Training Programs | $20,000 - $50,000 | Comprehensive training for compliance and efficiency |
Onboarding Expenses | $5,000 - $15,000 | Certification and background checks |
Operational Setup | $95,000 - $235,000 | Includes workforce management systems |
Startup Cost 7: Marketing & Branding Investment
Investing in marketing and branding is crucial for your biodiesel manufacturing business. This expense not only establishes your identity in a competitive market but also drives customer acquisition and retention. With costs typically ranging from $30,000 to $100,000, understanding the nuances of this investment can significantly impact your overall success.
Key Cost Drivers
The primary cost drivers for marketing and branding include brand development, digital presence, and public relations campaigns. These elements are essential for creating a strong market entry and ensuring long-term sustainability.
Factors Affecting Cost
- Quality of branding materials and design services
- Scope of digital marketing efforts, including website and social media
- Depth of market research and competitive analysis
- Complexity of public relations strategies and campaigns
Potential Cost Savings
Implementing effective cost-saving strategies can help manage your marketing budget. By focusing on targeted campaigns and leveraging digital tools, you can maximize your return on investment.
- Utilize social media for cost-effective outreach
- Engage in partnerships for shared marketing expenses
- Leverage analytics to refine marketing strategies
- Focus on organic growth through content marketing
- Implement referral programs to boost customer acquisition
- Negotiate with vendors for better rates on services
- Utilize free or low-cost marketing tools
- Track ROI to adjust spending effectively
Biodiesel Marketing & Branding Cost Breakdown
Expense Component | Estimated Cost | Notes |
---|---|---|
Brand Development | $30,000 - $100,000 | Includes logo design and identity creation. |
Digital Presence | $10,000 - $30,000 | Website setup and social media campaigns. |
Market Research | $5,000 - $15,000 | Competitive analysis and customer insights. |
Public Relations | $5,000 - $20,000 | Campaigns to enhance brand visibility. |
Advertising | $10,000 - $50,000 | Initial advertising investments for outreach. |